Paradigm Precision
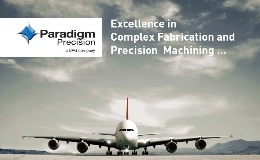
Paradigm Precision Headquarters Location
Tempe
About Paradigm Precision
Paradigm Precision specializes in the manufacturing of complex fabrication and precision machined components for gas turbine engines. We serve customers around the world in commercial and military aviation, power generation, the marine industry, rotary wing and unmanned aerial vehicles.
Our talented people apply their skills, knowledge and experience to provide quality products and services. Together, we've established 5 leading-edge capabilities that enable us to fabricate the most complex gas turbine engine components. These capabilities include the following:
- Materials
- Special Processes
- TCT Blast TM
- Process and Manufacturing
- Engineering Software
Today, we are trusted by OEMs, Risk and Revenue Sharing Partners, and operators in commercial aviation, military aviation, power generation, the marine industry, rotary wing and unmanned aerial vehicles (UAVs).
Material CapabilitiesOur talented people apply their skills, knowledge and experience to provide quality products and services. Together, we've established 5 leading-edge capabilities that enable us to fabricate the most complex gas turbine engine components. These capabilities include the following:
- Materials
- Special Processes
- TCT Blast TM
- Process and Manufacturing
- Engineering Software
Today, we are trusted by OEMs, Risk and Revenue Sharing Partners, and operators in commercial aviation, military aviation, power generation, the marine industry, rotary wing and unmanned aerial vehicles (UAVs).
Stainless Steel Alloys
Aluminum
High-Temp Nickel and Cobalt Alloys
Titanium
Special Process CapabililtiesAluminum
High-Temp Nickel and Cobalt Alloys
Titanium
Special Process Capabilities
Airflow Test & Measurement
Bonding
Brazing and Vacuum Heat Treat
EDM (Conventional Sinker, Wire, Fast-Hole Drilling)
Etching
Heat Treat
Investment Casting
Laser services (Cut, Weld, Hole Drilling-Effusion/Shaped)
NiCrAL Blast and Brush Nickel Electroplating
Surface Enhancement (Shot Peen, Glass Bead)
Thermal Coatings/Robotic Plasma Spray (Thermal Barrier, Hardface, LoK)
TCT BLAST™
Welding (TIG Plasma, Fusion, Resistance, Stud)
X-Ray
Conventional Machining as a Special Process (Turning, Hole Drilling, Edge Break)
Nondestructive Testing (Flourescent Penetrant)
TCT Blast TMAirflow Test & Measurement
Bonding
Brazing and Vacuum Heat Treat
EDM (Conventional Sinker, Wire, Fast-Hole Drilling)
Etching
Heat Treat
Investment Casting
Laser services (Cut, Weld, Hole Drilling-Effusion/Shaped)
NiCrAL Blast and Brush Nickel Electroplating
Surface Enhancement (Shot Peen, Glass Bead)
Thermal Coatings/Robotic Plasma Spray (Thermal Barrier, Hardface, LoK)
TCT BLAST™
Welding (TIG Plasma, Fusion, Resistance, Stud)
X-Ray
Conventional Machining as a Special Process (Turning, Hole Drilling, Edge Break)
Nondestructive Testing (Flourescent Penetrant)
TCT BLAST™ is a breakthrough process technology for the manufacture and repair of combustion chamber components.
The typical combustion chamber gas path requires a Thermal Barrier Coating (TBC), which performs the important function of insulating and protecting the parent metal from the severe heat load. Effusion hole air-cooling systems are used in conjunction with TBC to achieve maximum benefit by reducing the thermal gradients in the metallic substrate. This greatly reduces the driving force of thermal fatigue. Combustion chamber durability is improved dependent upon the integrity of the TBC ceramic insulation layer.
The current industry method used to produce effusion air-cooling holes in TBC-coated combustion chambers requires laser drilling through the metallic substrate and the TBC. Unfortunately, laser drilling generates significant fracture energy in the TBC, which results in TBC debonding, delamination and subsequent TBC loss. This, of course, adversely affects component durability and service life.
To solve this problem, we developed the TCT BLAST™, a proprietary process which enables TBC ceramic insulation to be applied after laser drilling of effusion air-cooling holes, thereby eliminating the laser damage which occurs from laser drilling through the TBC ceramic insulation layer.
There is also an additional benefit of this process. The metallic substrate air-cooling hole surfaces and edges are smoothed and rounded during the TCT BLAST™ process. This significantly improves the airflow characteristics of the air-cooling holes by increasing the hole Cd (discharge coefficient). Rigorous OEM testing (furnace cyclic and accelerated mission) has validated and verified the durability improvement which can be realized by using TCT BLAST™ process technology for manufacture and repair applications.
Process and Manufacturing CapabilitiesThe typical combustion chamber gas path requires a Thermal Barrier Coating (TBC), which performs the important function of insulating and protecting the parent metal from the severe heat load. Effusion hole air-cooling systems are used in conjunction with TBC to achieve maximum benefit by reducing the thermal gradients in the metallic substrate. This greatly reduces the driving force of thermal fatigue. Combustion chamber durability is improved dependent upon the integrity of the TBC ceramic insulation layer.
The current industry method used to produce effusion air-cooling holes in TBC-coated combustion chambers requires laser drilling through the metallic substrate and the TBC. Unfortunately, laser drilling generates significant fracture energy in the TBC, which results in TBC debonding, delamination and subsequent TBC loss. This, of course, adversely affects component durability and service life.
To solve this problem, we developed the TCT BLAST™, a proprietary process which enables TBC ceramic insulation to be applied after laser drilling of effusion air-cooling holes, thereby eliminating the laser damage which occurs from laser drilling through the TBC ceramic insulation layer.
There is also an additional benefit of this process. The metallic substrate air-cooling hole surfaces and edges are smoothed and rounded during the TCT BLAST™ process. This significantly improves the airflow characteristics of the air-cooling holes by increasing the hole Cd (discharge coefficient). Rigorous OEM testing (furnace cyclic and accelerated mission) has validated and verified the durability improvement which can be realized by using TCT BLAST™ process technology for manufacture and repair applications.
Paradigm Precision serves a global market though the delivery of highly specialized machined components.
Our strictly disciplined approach to engineering and manufacturing delivers value to our customers through our global operations, exceptional machine technology, specialized processes and certifications, Six Sigma and LEAN manufacturing expertise, and world-class engineering. In addition to our Core Capabilities, the following is a list of our Complimentary process capabilities:
5-Axis CBN grinding
Assembly and Sheet Metal Fabrication
Automatic Grit BLAST
Boring mills w/ 40-ton table capability
CNC Spark Erosion Grinding (Honeycomb)
Grinding (Surface, OD/ID, Jig)
Laser Services (Cut, Weld, Hole Drilling-Effusion/Shaped)
Milling - Horizontal, Vertical, 5-Axis, Multi-Pallet
Press Department (800T, 250T, 90T, 40T)
Repair Services (Full Life Cycle)
Super Plastic, Radial and Deep Draw/Hot Forming
Titanium Processing and Chemical Milling
Tool Design/Manufacturing
Turning - From under 1" to 240" in Diameter
Water Jet Metal Cutting (3-axis & 5-axis)
Welding (Plasma, Fusion, Resistance, Stud)
Metallurgical/Calibration Lab
Engineering SoftwareOur strictly disciplined approach to engineering and manufacturing delivers value to our customers through our global operations, exceptional machine technology, specialized processes and certifications, Six Sigma and LEAN manufacturing expertise, and world-class engineering. In addition to our Core Capabilities, the following is a list of our Complimentary process capabilities:
5-Axis CBN grinding
Assembly and Sheet Metal Fabrication
Automatic Grit BLAST
Boring mills w/ 40-ton table capability
CNC Spark Erosion Grinding (Honeycomb)
Grinding (Surface, OD/ID, Jig)
Laser Services (Cut, Weld, Hole Drilling-Effusion/Shaped)
Milling - Horizontal, Vertical, 5-Axis, Multi-Pallet
Press Department (800T, 250T, 90T, 40T)
Repair Services (Full Life Cycle)
Super Plastic, Radial and Deep Draw/Hot Forming
Titanium Processing and Chemical Milling
Tool Design/Manufacturing
Turning - From under 1" to 240" in Diameter
Water Jet Metal Cutting (3-axis & 5-axis)
Welding (Plasma, Fusion, Resistance, Stud)
Metallurgical/Calibration Lab
CALYPSO
CNC Program Optimization
Volumill
GageTrak
IMS/POST
IQS
PCDmis
ProE CREO 2.0
SolidWorks
Unigraphics NX 9.0
CNC Program Optimization
Volumill
GageTrak
IMS/POST
IQS
PCDmis
ProE CREO 2.0
SolidWorks
Unigraphics NX 9.0
Number of Employees in Paradigm Precision
1,001 to 5,000
Paradigm Precision Revenue
$25M to $100M (USD)
Industry